Clean Mind, Clean Hands
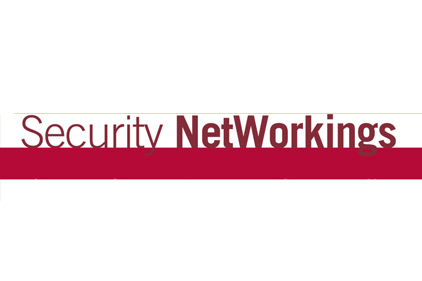
![]() |
Here, my $12,000 fusion splicer is suspended on a wall with duct tape while I replace broken fiber connectors. PHOTO COURTESY OF DAVE ENGEBRETSON |
For whatever reason — perhaps from growing up during the social revolution of the 1960s — I am a fairly consistent user of the seven words you can’t say on network TV. Whenever I’m cut off in traffic or a piece of equipment fails to perform exactly right, out comes a virtual waterfall of curse words. I pride myself on creative and flexible usage of these nouns and verbs, none of which will be published here. My daughter, however, has heard them all from her backseat position in the Jeep, and thankfully hasn’t yet picked up on this bad habit.
I recently taught a Sunday school class. The pastor had set me up with all of the materials including a video that I was supposed to pull from the Internet. So here I was in front of the class trying to connect my laptop to the projection screen and the Internet, and nothing worked. I fussed with the stuff for a few minutes, then gave up and told the class we were going old school — no videos, just talk.
My daughter attended the class, and as we were driving home I asked her how she liked the presentation. She said, “Daddy, I’m so proud of you. You didn’t swear once.” Oh yeah, Father of the Year material right there.
Which brings me to a recent project I’ve been working on: training the electricians at one of the Big Four automobile manufacturers’ stamping plants. Fiber optics is entering the life safety arena, and this factory is having a voice evacuation system installed by SimplexGrinnell that required multimode fiber links from module to module around eight locations in the building complex that measures roughly one-third of a mile square. I’ve been training the electricians on fiber optic terminations using a fusion splicer, optical time domain reflectometer (OTDR), and optical loss test set.
Ideally, when terminating and testing fibers the environment would be extremely clean; think hospital surgery room. Any small speck of dirt on a connector face can cause a complete failure of the light signals to pass from one cable to the next.
Because this factory has been up and running since the 1960s, every surface in the buildings is covered in that fine blend of greasy dirt that means America has been building something. Because of this dirt, both the fusion splicing and testing of the fibers was very time-consuming. I found that just handling the cables caused my hands to be extremely dirty after just a few minutes; it was impossible to keep them clean as the nearest restroom was usually a golf cart ride away. After splicing the connectors on the six-strand multimode fibers we would test them, and when “good” we would tape them temporarily to the side of the box until all were done, which is when the fun and swearing began.
One of the problems was that the factory had purchased 250-micron loose-tube fiber cable, which is OK except they had bought termination boxes built for 900-micron jacket fibers. As a micron is one-millionth of a meter, a 250-micron fiber is approximately three times the diameter of a human hair. Not only do these fibers get easily tangled together, but they are extremely fragile and will break on contact with any sharp edge or object, such as the sides, top, bottom, and inside cable management holders within the metal termination boxes. So we would often have to re-splice and replace connectors that were broken off during the process of placing the cables and connectors into the boxes. At one point my $12,000 fusion splicer was hanging off the wall, eight feet in the air, supported by two strips of duct tape, while I stood on a ladder and replaced a connector. This created another opportunity for colorful language.
Once the splices and connectors were in the box, testing was performed on each and every cable. Here is where I was reminding others about the cleanliness needed for proper fiber work. We would test a cable and it would show “dead” — for example, that the connector or fusion splice was broken. We then would re-clean the end of the testing connector with common adhesive tape, and often the retest would show that the connector and splice were perfectly OK. Even a 5- or 10-micron sized speck of dirt can stop the signal. We also found in some cases that dirt from the test lead transferred to the installed connector, requiring the thorough cleaning of both connector faces before the fiber would pass the test.
What lessons were learned? First, fiber optics is coming into our business whether we like it or not, and security integrators will need to have their technicians properly trained and equipped with fiber tools and testers so they can install and troubleshoot fiber links. Buy the right termination boxes for the type of fiber you are installing. And for those practitioners of four-letter words, there will be plenty of opportunities to step up your game if you don’t keep the fiber connector ends clean.
Live Training |
Through the miracle of the Internet, I can now invade your home or business and provide networking and fiber optic training right at your desktop. With the sponsorship of Axis Communications, I am again partnering with ADI to present a live webinar training series. The “Get the Picture: Easy IP Programming for Ethernet Cameras and Devices” 4-hour webinar will be first presented on Feb. 21, with other presentations planned throughout 2012. Just call your local ADI and use the part number 3X-IPWEBTRN to register. Cost is only $59 and you get a free copy of my latest book. If you’re new to IP this is a great and inexpensive way to get started. |
Looking for a reprint of this article?
From high-res PDFs to custom plaques, order your copy today!