West Penn Wire Fiber Connectors Easy to Install
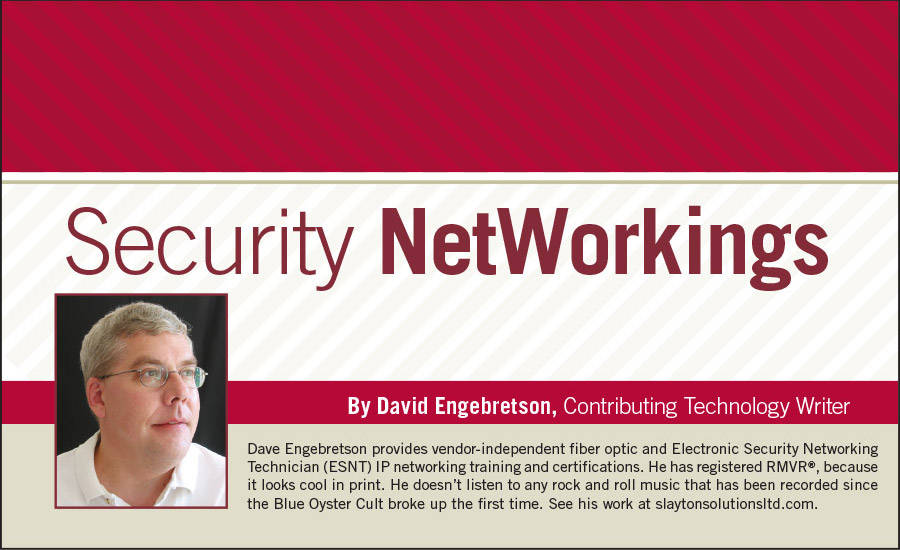
In the past 15 years I have provided fiber optic training and certification for hundreds of technicians from many different industries — I even trained the technicians who operate the container ship cranes at the Long Beach Harbor in California.
The technology used in fiber optic communications has stayed pretty much the same since the beginning of this century. Fiber cables properly installed and terminated in 1998 will work just as well as new cables installed today, with one notable exception. In short distance (less than two miles) fiber runs, most end users and contractors are now installing multimode fiber strands that have a 50 micron core and are laser optimized. Older multimode fiber had a 62.5 micron core.
Laser optimized 50 micron fiber has become the de facto standard for short distance fiber installations because it can support up to 40 Gbps Ethernet. Because the fiber is made of glass, it doesn’t corrode or deteriorate over time. A cable that is properly installed and terminated should provide decades of service.
The key phrase in the above paragraph is “properly … terminated.” The installation of fiber optic connectors is absolutely critical to the overall performance of a particular fiber link. Poor connector installation equals poor (or no) communications over that fiber.
Factory-installed connectors are usually produced using a “glue-and-polish” process. Automated machines glue stripped fiber ends into connector bodies so that they stick out of the tip (or ferrule) of the connector. Then the connector ends are polished using progressively finer grades of sandpaper to achieve a high quality and low-loss connector.
The same glue-and-polish technique has been done manually by field technicians over the past 25 years. While skilled technicians can put this type of connector on fairly rapidly, those techs that don’t get regular practice will often have problems, adding time and aggravation to installations.
There is another way to produce quality connectors: the “cleave-and-crimp” connectorization method where a fiber end is stripped, or “cleaved,” using a special tool, and inserted into the back of a connector that already has a polished tip end that was installed at the factory. This is a much faster way as connectors can be installed in minutes.
The main drawback to the cleave-and-crimp connectors is that it was impossible to verify the quality of the connector until both ends were installed and an optical loss test set (OLTS) was used to test the completed fiber link. If the test failed, the technician basically had to guess which end was bad, cut off the connector and replace it, then test again.
To overcome this issue of knowing whether a connector is good or not, West Penn Wire produced its Brilliance line of connectors. An installer using the Brilliance connector installation kit can see a visible laser through the opaque Activator switch that is opened to accept the inserted fiber end, and is then closed, clamping the fiber into place.
Once the technician verifies that the laser light has gone out, sliding the activator tab back to its starting position clamps the fiber end into the connector, and the deed is done.
The Brilliance connectors also have a unique capability in that the activator tab can be opened, the existing fiber link end removed, and a newly prepared fiber end can be inserted, verified and clamped as described above.
In my extensive testing of these connectors I have found that they are extremely easy to install, and the laser light verification works great. The Brilliance connectors are a breakthrough in fiber technology that can help technicians spend less time connecting fibers and build their confidence. For information on West Penn Wire’s complete line of copper and fiber optic products visit www.westpenn-wpw.com.
Do you like reading Dave’s column? You can read each one in the archives.
Looking for a reprint of this article?
From high-res PDFs to custom plaques, order your copy today!